Carbon Footprint For The BMW i7 Electric Sedan Is Low
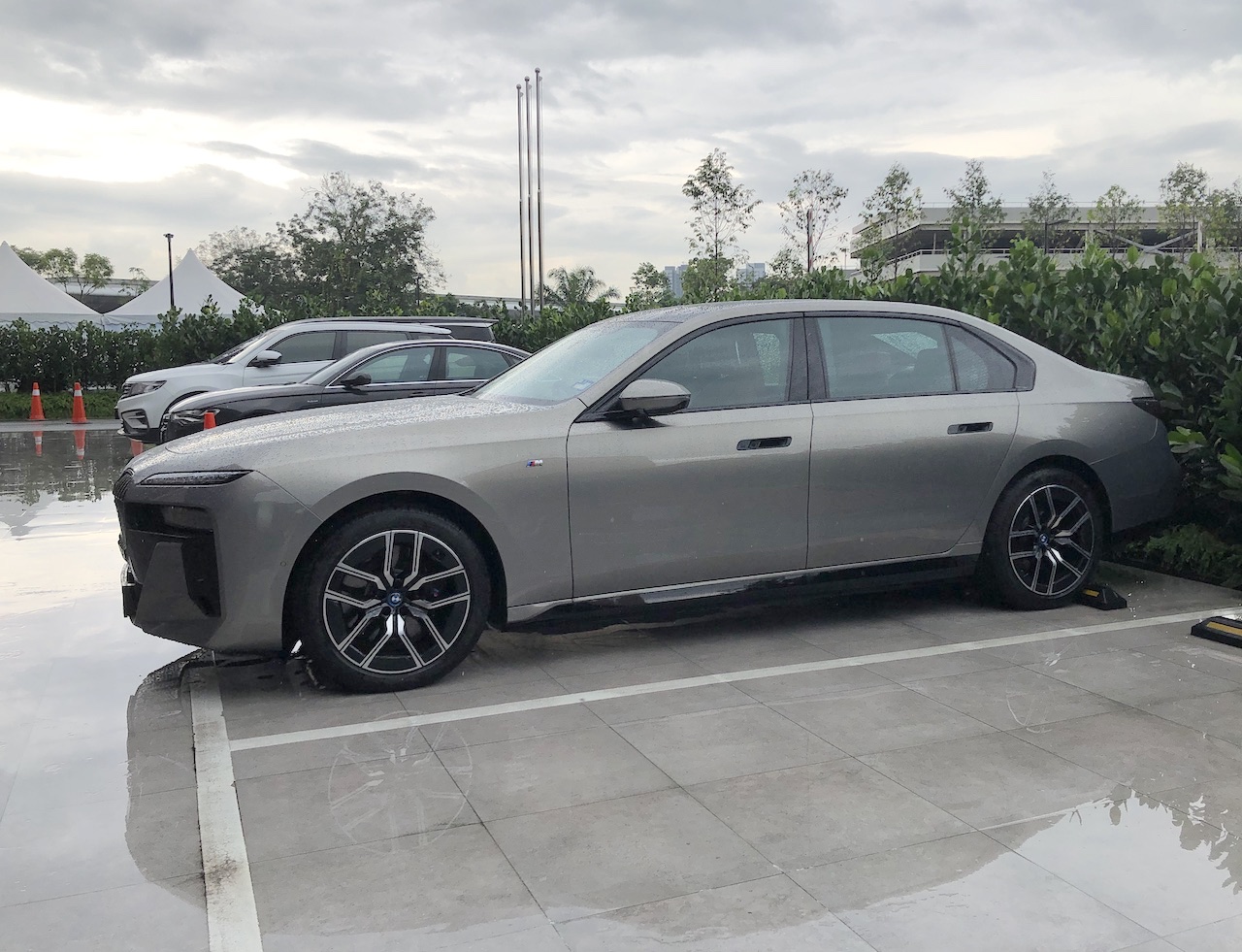
BMW i7 with its purely electric drive system.
The arrival of a fully electrified flagship sedan for the BMW range shows how the BMW 7-Series range will soon be void of petrol powered variants.
This is the most valuable contribution to accomplishing the sustainability goals and underlines how BMW is endeavoring to cut carbon emissions in the use phase of the entire fleet and across all segments by a further 50 percent by 2030 (compared with the figure for 2019).
The global warming potential of the BMW i7 xDrive60 throughout its lifecycle is around 33 / 39 per percent lower respectively than that of the new BMW 740i xDrive / BMW 740i when using the current EU electricity mix.
If renewable power is used for charging, the difference in lifecycle global warming potential increases even further to around 60 / 64 percent respectively.
The carbon footprint for the new BMW i7 will be stated in a validation certificate endorsed by independent auditors by the time production starts in July 2022.
A particularly rigorous approach is taken to reducing the CO2 emissions released during production of the fifth-generation BMW eDrive technology fitted in the new BMW i7.
In the supply chain alone, utilizing green electricity for battery cell production and making increased use of secondary raw materials cuts CO2 emissions by around 20 per percent compared with a vehicle where these measures are not deployed.
Responsible raw materials production
The sustainability targets defined for all model variants in the new 7-Series range also include the upstream production chains. The BMW Group has undertaken to create the most sustainable supply chain anywhere in the automotive industry.
The focal points on the purchasing side are compliance with environmental and social standards, respect for human rights, conservation of natural resources and reduction of CO2 emissions. Measures for optimizing sustainability are therefore established in consultation with suppliers, such as using secondary raw materials and harnessing renewable energy.
Besides an eco-friendly manufacturing process, consideration is also given here to the recyclability of the component in question and to health-related aspects. The checks also include ensuring that potentially allergenic materials, such as nickel, are not used in areas where they could be touched by customers.
This holistic approach to improving sustainability also embraces those technological developments that make it possible to reduce the use of critical materials, or even dispense with them altogether.
For instance, a design principle has been devised for the electric motors forming part of the fifth-generation BMW eDrive technology in the BMW i7 (which are also manufactured at BMW Group Plant Dingolfing alongside the car) that eliminates the need to use rare-earth metals in the rotor.
Instead of the customary magnets for which these raw materials are needed, an electrically excited rotor is used to ensure both instantaneous and precisely controllable actuation of the electric drive.
The BMW Group has thereby capitalized on its industry-leading development and production expertise in the field of drive systems to enable it to manufacture electric motors irrespective of the availability of critical raw materials.
The BMW Group procures the cobalt required to manufacture the battery cells itself, before making it available to the battery cell suppliers. This gives the company complete transparency with regard to the material’s origin and the mining methods used.
Although no cobalt from the Democratic Republic of the Congo (DRC) is being used in the battery cells for fifth-generation BMW eDrive technology, the BMW Group is following the principle of “empowerment before withdrawal” by participating in a local project there.
The company, together with its partners, has commissioned the German Agency for International Cooperation (GIZ) to develop measures aimed at improving working and living conditions for both artisanal mine workers and the inhabitants of nearby communities.
If the project is successful, having cobalt supplied directly from the DRC could become an option for the BMW Group once more.
Lithium is another raw material that is vital for the production of high-voltage batteries but classified as critical. The BMW Group again sources this raw material directly before supplying it to battery cell manufacturers.
This ensures complete transparency regarding its origin. In 2019, the BMW Group already signed a supply agreement for lithium from hard-rock deposits in Australian mines.
Since 2022, the company has additionally been procuring lithium from Argentina, where this raw material is extracted from the saline water in salt lakes using an innovative technique, minimizing the impact on local ecosystems and communities.
The BMW Group has also commissioned two prestigious American universities to carry out a study into sustainable lithium extraction in Latin America. The aim of the study is to investigate the impact of lithium extraction on local water supplies.
The all-electric luxury sedan is a fully integrated member of the 7-Series line, and clearly demonstrates how an exclusive driving experience and the ultimate feeling of on-board wellbeing can be combined with an unwavering commitment to sustainability.