Toyota Has Showcased Its New Cutting Edge EV Production Line
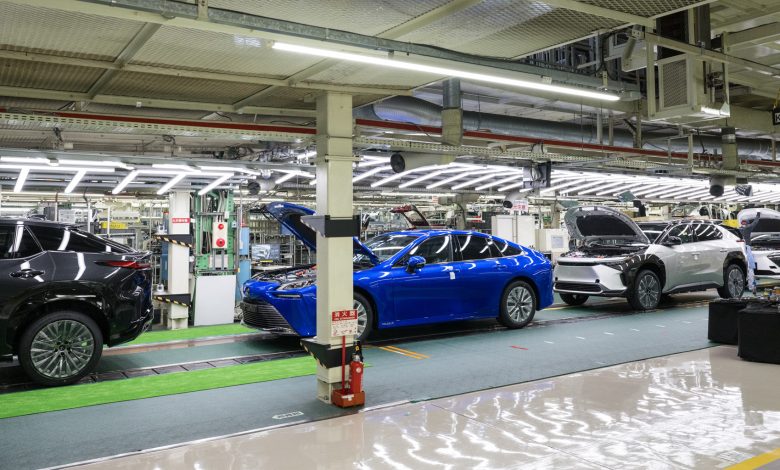
This new production line is touted by Toyota to cut EV manufacturing time from hours to minutes.
While it is certainly true that Toyota might be on the back foot currently in the EV space, its current deficit will likely not remain so for very much longer. That is as apart from having not too long ago announced some rather ambitious goals on producing solid state drive batteries by 2027, the Japanese manufacturer today has also shown off its new next-generation battery electric vehicle production line. And boy, what an incredible bit of tech it is…
Getting straight into the meat and potatoes of it first, the one big tech toy that Toyota has showcased with this new production line is its giga-casting feature. Giga-casting is the process of pouring molten aluminium into a mould, but as the name implies, this mould is to be rather large.
How large? Well the giga-casting process showcased by Toyota recently at its Myochi plant in Japan produced the entire rear third of a vehicle’s chassis as one single piece. Though perhaps even more impressive than that is for this entire process to take just 3 minutes from start to finish, relative to the 86 parts, 33 steps, and several hours the Japanese automaker quotes for creating the same piece using conventional methods.
Now of course, Tesla fanboys will be commenting that the American EV automaker has been using this giga-casting technology for a while already. What makes the Toyota system slightly more innovative than what was developed at Fremont however is its proprietary analysis technology to improve the quality of the castings and to reduce the number of defective products, which should lead to fewer quality control issues for the Japanese automaker relative to its Californian counterpart.
Moreover, Toyota has apparently designed its future BEV lineup around this new giga-casting process to maximise the production time saving from it. Nearly all future mainstream Toyota BEVs will supposedly share a three-part modular structure for the front, center, and rear. In the spirit of kaizen (continuous improvement) too, Toyota has been continually refining its giga-casting process since the first prototype was built in September 2022, with the automaker eventually aiming for a 20% higher productivity than its competitors using this new technology.
Continuing on the topic of higher productivity meanwhile, Toyota has also been implementing other less showy innovations to improve the efficiency of its BEV manufacturing too. Among the new ideas for instance is taking advantage of the fact that these all-electric cars can be safely run indoors, and developing a production line in which vehicles on said line will move under its own steam while being guided by sensors as it is being put together.
Toyota’s new next-gen production line is currently earmarked for only a few of its Japanese factories at this time, but it is likely that this new manufacturing system will make its way internationally too, as the automaker is currently aiming to produce 1.5 million EVs annually from 2026. So while it may have taken a good long while, the sleeping giant of the auto industry is now all fully rearing to go in the BEV race. Watch out, Tesla.