EV Battery Technology Needs To Be Organic And Recyclable
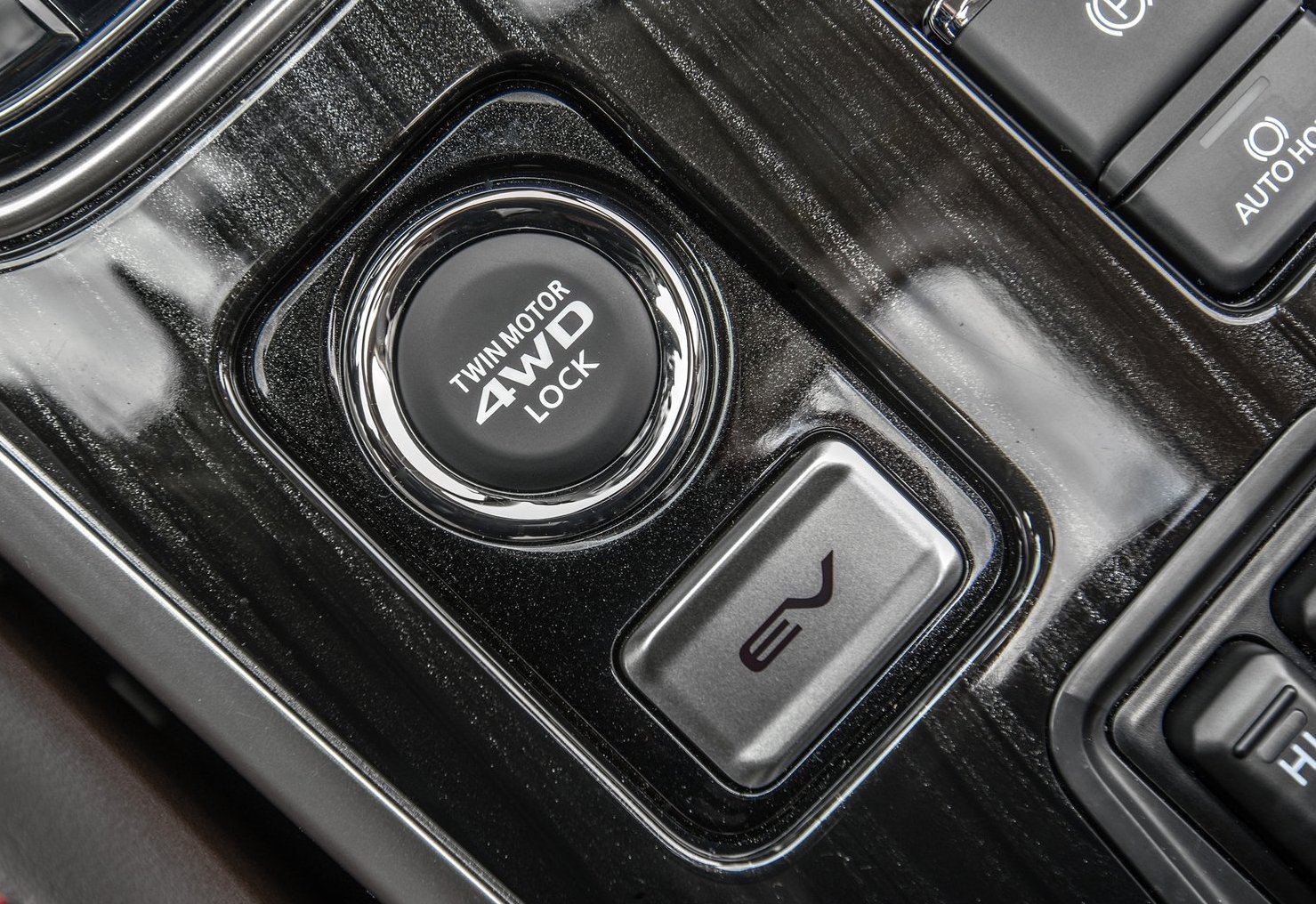
The world has been reset by forces unexplainable and we should start thinking about how to stop further destruction of our home, earth. The advancements in electric vehicle technology and the push by very developed nations to get more electric cars on the road means the increased production of electric vehicle batteries and this increase mining for the raw materials needed to make batteries and the idea on how to dispose of these worn batteries in the future.
Battery technology in its simplest form dates back more than two centuries. The word itself is an umbrella term since batteries come in all shapes and sizes: lead-acid, nickel-iron, nickel-cadmium and nickel-metal hydride.
Lithium-ion batteries which itself can be a catchall term were first developed in the 1970s, and first commercialized by Sony in 1991 for the company’s handheld video recorder. They are now found in everything from smart phones to medical devices to aeroplanes to the international space station.
The primary reason why electric vehicles are still relatively expensive is the cost of the raw materials required in their production. In addition to lithium, other minerals like cobalt and graphite are needed for lithium-ion batteries, as well as metals like nickel, aluminum and manganese. Electric vehicles now outpace consumer electronics in the demand for lithium.
Daimler is working on advanced, ‘organic’ electric vehicle (EV) battery technology. The company describes the technology as ‘very promising’ but it will be at least 15 years before to is viable for series production in cars available to consumers. Andreas Hintennach, Mercedes’ senior manager of battery research, said, “It’s a very promising technology. I’ve already seen it working in laboratories, where the results look really good, but we don’t see that it’s close to being used in production technology for now. It’s around 15-20 years away.”
Significance: Daimler has already debuted the technology in concept form in the Mercedes-Benz Vision AVTR sport utility vehicle (SUV). These ‘organic’ battery chemistries use graphene-based organic cell chemistry. Graphene is a very flexible and highly conductive new material that was developed originally at Manchester University in the United Kingdom and which has an enormous number of potential applications.
This new and still highly experimental form of battery chemistry dos not use any rare earths or metals, and therefore means that batteries can actually be ‘composted’ and are entirely recyclable. It also gets rid of the need to use rare earth materials like lithium and cobalt, which have significant issues with ethical sourcing and supply.
In addition to an exponentially high energy density when compared to today’s battery systems with up to 1,200 Wh/litre, the technology also impresses with its exceptional fast charging capability via automated, conductive charging technology. This means that the battery will be fully recharging in less than 15 minutes. The innovative technology also allows maximum flexibility with regard to the construction space: with a local minimum of 94 millimetres, the battery adapts ideally to the shared space vehicle concept, thus maximising the multifunctional interior.
With a capacity of around 110 kWh, the VISION AVTR enables an electric range of more than 700 kilometres. By recuperating during roll-out and braking, the high-voltage battery can be recharged with a higher efficiency than established systems while driving and thus contributes to the high energy efficiency of the overall system.