புகாட்டி 3D டைனிங் பிரேக் கல்பீப்பர் சாத்தியம் என்று நிரூபிக்கப்பட்டது
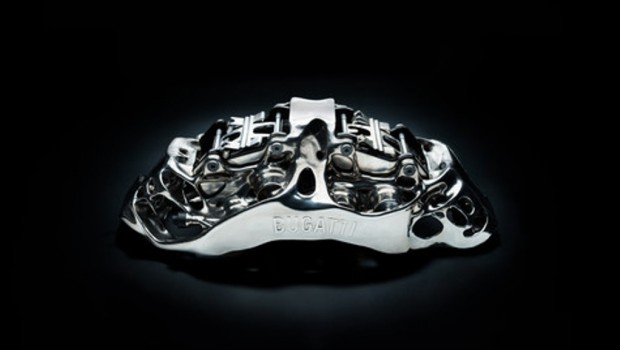
முதல் முறையாக, புகாட்டி டெவலப்பர்கள் 3-D அச்சு மூலம் தயாரிக்கப்படும் ஒரு பிரேக் கூப்பரை வடிவமைப்பதில் வெற்றியடைந்தனர். டைட்டானியம் இருந்து புதிய பிரேக் கருவி தயாரிக்கப்படுகிறது, அலுமினியம் உள்ளது தேதி வாகன கூறுகள் சேர்க்கை தயாரிப்பு பயன்படுத்தப்படும் முக்கிய பொருள்.
இது, டைட்டானியத்திலிருந்து 3-D அச்சிடும் செயல்முறைகளைப் பயன்படுத்தி உற்பத்தி செய்யும் உலகின் மிகப் பெரிய செயல்பாட்டு கூறு ஆகும்.
புகாட்டி தற்போது புதிய சிரோன் மீது மிக சக்தி வாய்ந்த பிரேக்குகளை பயன்படுத்துகிறது. பிரேக் கால்லிபர்கள் ஒரு முற்றிலும் புதிய அபிவிருத்தி. அவர்கள் அதிக வலிமை அலுமினியம் அலாய் ஒரு தொகுதி இருந்து போலி. எல் டைட்டானியம் பிஸ்டன்கள் ஒவ்வொன்றும் முன் அலகுகளாகவும், பின்புறான ஒவ்வொரு அலகுகளில் ஆறுகளாகவும் உள்ளன, இவை தற்போது உற்பத்தி வாகனம் மீது நிறுவப்பட்ட மிகப்பெரிய பிரேக் கால்ஃபிர்களாகும். சியோனின் பிரேக் கால்ஃபிர்கள் ஒரு இயற்கை மாதிரியின் அடிப்படையில் பயோனிக் கோட்பாடுகளை பயன்படுத்தி உற்பத்தி செய்யப்படுகின்றன. புதிய கட்டிடக்கலை குறைந்தபட்ச எடை அதிகபட்ச விறைப்புடன் ஒருங்கிணைக்கிறது. பிரேக்க்களின் வடிவமைப்பு மற்றும் இயக்க முறைக்கான உத்வேகம் மோட்டார்களிலிருந்து எடுக்கப்பட்டது.
3-D அச்சுப்பொறியிலிருந்து புதிதாக உருவாக்கப்பட்ட டைட்டானியம் பிரேக் கருவி மூலம், புகாட்டி இப்போது ஒரு படி மேலே சென்று புதிய தரையை உடைத்து வருகிறது. இந்த குறிப்பிட்ட டைட்டானியம் அலாய், Ti6AI4V வின் அறிவியல் பெயருடன், முக்கியமாக விண்வெளி தொழில் நுட்பத்தில் பயன்படுத்தப்படுகிறது, உதாரணமாக மிகவும் வலியுறுத்தப்பட்ட அண்டர்கிரேஜ் மற்றும் பிரிவு பிரிவுகளுக்கு அல்லது விமானம் மற்றும் ராக்கெட் என்ஜின்களில் பயன்படுத்தப்படுகிறது. பொருள் அலுமினியத்தை விட அதிக செயல்திறனை வழங்குகிறது. உதாரணமாக, ஒரு 3-D அச்சிடப்பட்ட கூறு கூட, அது 1,250 N / mm2 ஒரு tensile வலிமை உள்ளது. இதன் அர்த்தம், 125 டிகிரி செல்சியஸ் சக்தியைப் பயன்படுத்தி, இந்த டைட்டானியம் கலவையின் சதுர மில்லிமீட்டருக்கு பொருந்துகிறது. புதிய டைட்டானியம் பிரேக் கூப்பர், இது 41 செ.மீ. நீளம், 21 செ.மீ அகலம் மற்றும் 13.6 செ.மீ. உயரம் கொண்டது, 2.9 கிலோ எடை கொண்டது. தற்பொழுது 4,9 கிலோ எடையுள்ள அலுமினிய கூறுகளுடன் ஒப்பிடுகையில், புகாட்டி புதிய பங்கைப் பயன்படுத்துவதன் மூலம் அதிகபட்ச வலிமையை உறுதிப்படுத்தும் அதே நேரத்தில் சுமார் 40% பிரேக் எரிபொருளின் எடை குறைக்க முடியும்.
இன்றைய தினம், இந்த அணுகுமுறை சாத்தியமற்றதல்ல என்பதால், டைட்டானியம் தொகுதிகளில் இருந்து ஆலை அல்லது கள்ளு கூறுகளை கூட சாத்தியமற்றதாகவோ அல்லது சாத்தியமற்றதாகவோ இருக்கலாம், ஏனெனில் அலுமினியத்துடன் கூடிய பொருள் மிக அதிகமான வலிமை காரணமாக உள்ளது. இந்த சிக்கல் இப்போது மிக உயர்ந்த செயல்திறன் கொண்ட 3-டி அச்சுப்பொறியைப் பயன்படுத்தி தீர்க்கப்பட்டு வருகிறது, இது மேலும் சிக்கலான கட்டமைப்புகளை உருவாக்கும் சாத்தியத்தை திறக்கிறது, இது எந்த வழக்கமான உற்பத்தி செயல்முறையுடன் சாத்தியமானதாக இருப்பதை விட குறிப்பிடத்தக்க வகையில் வலுவானது மற்றும் வலுவானதாக இருக்கிறது.
3-D- அச்சிடப்பட்ட டைட்டானியம் பிரேக் கருவிக்கான வளர்ச்சி நேரம் மிகவும் குறுகியதாக இருந்தது. முதல் யோசனை முதல் அச்சிடப்பட்ட கூறு வரை, அது மூன்று மாதங்கள் மட்டுமே எடுத்துக்கொண்டது. அடிப்படை கருத்து, வலிமை மற்றும் விறைப்பு உருவகப்படுத்துதல்கள் மற்றும் கணக்கீடுகள் மற்றும் வடிவமைப்பு வரைபடங்கள் ஆகியவை லாகர் ஜென்ட்ரம் நோர்ட்டிற்கு புகாட்டி மூலம் முழு தரவு தொகுப்பாக அனுப்பப்பட்டன. இந்த நிறுவனம் பின்னர் செயல்முறை உருவகப்படுத்துதல், துணை அமைப்புகளின் வடிவமைப்பு, உண்மையான அச்சிடுதல் மற்றும் கூறுகளின் சிகிச்சை ஆகியவற்றை நடத்தியது. புகாட்டி முடிக்க வேண்டிய பொறுப்பு.
திட்டத்தின் தொடக்கத்தில் டைட்டானியம் பொருத்தமான உலகில் மிகப்பெரிய அச்சுப்பொறி இது லேசர் ஜெண்ட்ரம் நோர்டில் சிறப்பு 3-டி பிரிண்டர், நான்கு 400 வாட் லேசர்கள் கொண்டிருக்கிறது.
ஒரு பிரேக் காலிபர் அச்சிட மொத்தம் 45 மணி நேரம் ஆகும். இந்த நேரத்தில், டைட்டானியம் தூள் அடுக்கு மூலம் அடுக்கு வைக்கப்பட்டது. ஒவ்வொரு அடுக்குகளிலும், நான்கு லேசர்கள் பிரேக் காலிபர் வரையறுக்கப்பட்ட வடிவத்தில் டைட்டானியம் தூள் உருகுவதால். பொருள் உடனடியாக குளிர்ந்து மற்றும் பிரேக் காலிபர் வடிவம் எடுக்கிறது. தேவையான அடுக்குகளின் எண்ணிக்கை 2,213 ஆகும். இறுதி அடுக்கு முடிந்ததை தொடர்ந்து, மீதமுள்ள மீதமுள்ள டைட்டானியம் தூள் அறையிலிருந்து அகற்றப்பட்டு, மூடிய சுழலில் மீண்டும் சுத்தம் செய்யப்பட்டு பாதுகாக்கப்படுகிறது. அறையில் எஞ்சியிருக்கும் பிரேக்கிங் கால்பேர், அதன் உறுப்புகளை பராமரிப்பதுடன், அதன் வெப்பத்தை நிலைநிறுத்துவதையும் அதன் இறுதி வலிமையை அடைந்து வருவதையும் உறுதிப்படுத்துகிறது.
பிரேக் காலிபர் 700 ° C முதல் வெப்பநிலையை வெளிப்படுத்தும் ஒரு உலைகளில் வெப்ப சிகிச்சை மேற்கொள்ளப்படுகிறது, இது 100 ° C வீழ்ச்சிக்கு வழிவகுக்கும், எஞ்சியிருக்கும் மன அழுத்தத்தை அகற்றவும் மற்றும் பரிமாண நிலைத்தன்மையை உறுதி செய்யவும். இறுதியாக, ஆதரவு அமைப்புகள் நீக்கப்பட்டன மற்றும் கூறு தட்டில் இருந்து பிரிக்கப்பட்ட. அடுத்த உற்பத்தி நிலையில், மேற்பரப்பு ஒரு ஒருங்கிணைந்த இயந்திர, உடல் மற்றும் வேதியியல் செயல்முறைகளில் மென்மையாக்கப்படுகிறது, இது அதன் சோர்வு வலிமையை கடுமையாக மேம்படுத்துகிறது, அதாவது பிந்தைய வாகன செயல்பாட்டில் உள்ள உறுப்புகளின் நீண்டகால ஆயுள். இறுதியாக, பிஸ்டன் தொடர்பு மேற்பரப்புகள் அல்லது நூல்கள் போன்ற செயல்பாட்டு பரப்புகளின் வரையறைகளை, ஐந்து அச்சில் அரைக்கும் இயந்திரத்தில் இயக்கப்படுகிறது, இது அதன் வேலை முடிவதற்கு மற்றொரு 11 மணி நேரம் ஆகும்.
உற்பத்தி வாகனங்களில் பயன்படுத்த முதல் சோதனை ஆண்டு முதல் பாதியில் நடைபெறும்; கால அட்டவணையினை இன்னும் இறுதி செய்ய வேண்டும். அந்த கட்டத்தில், பொறியியலாளர் உற்பத்திக் காலத்தை கணிசமாகக் குறைக்க முடியும் என்பதையும், குறிப்பாக இயந்திரமயமாக்க முடியும் என்பதையும் பொறியாளர் உறுதிபடுத்துகிறார்.